Attracting and retaining talented young people into the mining sector is one of the industry’s biggest challenges. In February 2023 (when the Australian Bureau of Statistics last published data), there were over 10,400 vacancies in the sector – a 3% shortfall.1
This talent shortage is having a serious impact on the sector. One industry research report found that 71% of mining leaders believe the shortage is holding them back from delivering on their production targets and strategic objectives.2
The majority (86%) of mining executives also say it is harder to recruit and retain the talent they need compared with just two years ago. This is particularly the case in specialised areas like mine planning, process engineering, data science and automation.3
Why aren’t more young graduates entering the sector?
Despite the fact mining organisations are gradually moving away from traditional processes and embracing digital transformation – and taking steps to proactively improve sustainability – the sector still has somewhat of an image problem. For many young graduates, mining and minerals is seen as a dated sector with limited options for career advancement.
John Vagenas, Managing Director at Metallurgical Systems, says this is a perspective he would like to change.
“In reality, it’s actually a very exciting time to be in mining and minerals. Demand for resources isn’t going anywhere. As an industry we just need to leverage the proven technology that already exists and embrace sustainable and innovative digital tools to deliver the materials upon which we all depend”, he says.
“This means there is enormous scope for young people who want to make a difference and carve out a really exciting career,” he adds.
How is Metallurgical Systems making a difference?
The team at Metallurgical System is very passionate about creating pathways to encourage bright, young people to choose a career in mining and minerals. One way in which we do this is through our Internship Program, where we offer paid employment for quality candidates while they are completing their studies. Some of these interns then go on and continue to work for Metallurgical Systems.
“We believe very strongly in providing paid internships where candidates can not only earn an income while studying, but also learn practical and technical skills that will be of huge benefit in their future career,” says John.
Meet Joshua Chapman, Metallurgical Systems’ most recent intern
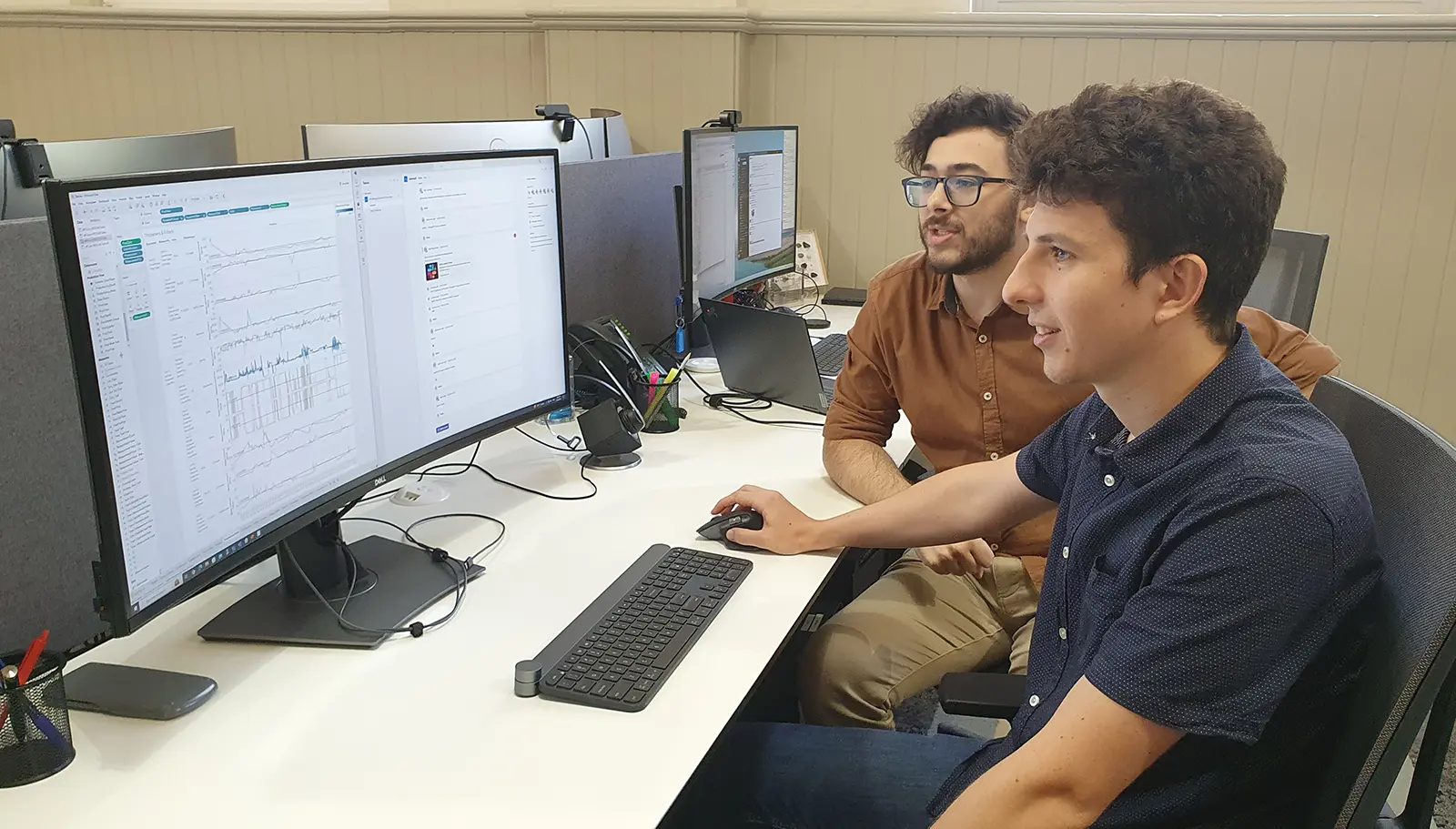
Joshua has recently undertaken an internship while completing a Bachelor of Chemical Engineering at the University of NSW, and says the experience has helped him refine and practice the skills he is acquiring as part of his study.
“All of the projects I worked on at Metallurgical Systems relate directly back to my degree, especially the model development, which allowed me to practice the design processes that have been drilled into me since my first year of study,” he says.
“Coming into my internship I really wasn’t sure what to expect. Previous intern experience had taught me some basics of process engineering, but this experience really enabled me to go deeper. I could never have anticipated the world of data capture and analysis that Metallurgical Systems introduced me to,” he says.
For Joshua, a key benefit of the experience was the chance to work with a highly knowledgeable and skilled team.
“Metallurgical Systems helped me to achieve all I set out to do, and more! I received amazing help and assistance from other engineers and staff at Metallurgical Systems who were always willing to lend a hand and teach me. I also had various projects to work on such as steady state model development, data report creation and even some software development,” he says.
“One of my key learnings was the significance of accurate process data and how it can be used to optimise and troubleshoot a process. I worked with data extensively throughout my internship. I learnt how to use databases to generate functional reports and troubleshoot problems with both simulated and real processing plants,” he adds.
Joshua spent a lot of his time at Metallurgical Systems developing a steady state model that could be used as part of Metallurgical Systems’ MI® Scenario software.
“The model can be used to run scenarios using this software, allowing a user to experiment with different simulated environments to run their plant in. The model was made for a lithium processing plant and I learnt many important lessons about the design process and simulation software used to create the model. I was delighted with the result of this model and proud of what I achieved,” he says.
“I surprised myself with how much I achieved during my internship. I finished a steady state model for use in a real plant, created multiple reports for clients all over the world and gained a deeper understanding into the importance of data in this field.”
At the end of his internship, Joshua was offered a position in the team next year.
“I am so excited to continue my journey at Metallurgical Systems as I complete my final year of university, with all these new skills under my belt,” he says.
Could you be our next intern? Want to learn more?
If you are interested in learning more about Metallurgical Systems and our internships, please get in touch.
References