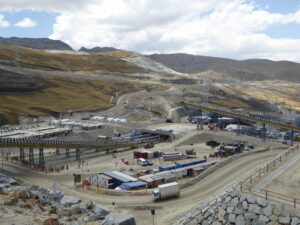
Test scenarios and optimise plant performance with confidence
From geopolitics to environmental concerns, cost optimisation to mineral scarcity, the mining and minerals sector is under more pressure than ever to do more with less. Yet making changes to plant processes can carry big risks and materially impact business models.
Scenario testing presents an opportunity to use the massive volumes of data generated in a plant to explore ‘what if’ scenarios. From these insights, leaders can make more informed decisions about how to optimise outcomes. Leading minerals process plants are using scenario testing to solve for big issues like ESG reporting and greenhouse gas emissions, productivity, forecasting and cost control, as well as more granular metrics like reagent quantities, altered flowsheets and other production variables.
According to the global Task Force on Climate-related Financial Disclosures (TCFD), scenario analysis is a key tool to help companies understand and quantify the risks and uncertainties of different hypothetical futures.
When it comes to climate scenarios — which can be particularly complex given timescales, scientific models, and the multi-faceted nature of consequences — choosing the right scenario testing tool proves critical. You need a tool that can test scenarios to reduce Scope 1, 2 and 3 emissions; one that can test everything from the impact of replacing fossil fuels with biomass, to using recycled instead of virgin materials.
That’s where Metallurgical Intelligence comes in. Our proven, industry-leading scenario testing solution — MI Scenario® — enables powerful analysis and testing of an endless range of variables and scenarios, helping you optimise operations and hit your ESG targets with confidence.
Scenario testing is all about answering ‘what if’ questions with absolute certainty. Questions like, what if we increase throughput? What if we add in another tank? What if we target a higher grade? What if a reactor goes offline or equipment fails? Or, if we made this change to our suppliers, could we reduce our greenhouse gas emissions?
MI Scenario® is an optional module in the award-winning MI Core® process digital twin solution from Metallurgical Systems. It uses a customised steady-state plant simulation model to predict the future for your plant by combining data from the past with known or expected upcoming changes in processing conditions. It can accurately determine potential outcomes to any modifications you propose — helping you make accurate, cost-effective and informed decisions about the way you run your plant.
By pairing our proven scenario testing solution with a process digital twin, process optimisation tool, or asset utilisation tool, you can further optimise plant performance.
increased recovery
reduction in reagent usage