How to use modern digital tools to exceed metal accounting governance requirements
The AMIRA P754 Code of Practice provides the framework for best practice metal accounting governance. It has gained widespread adoption as the recognised standard for metallurgical accounting practices across the mining and minerals sector.
The sector’s technological landscape has evolved significantly since the Code’s creation in 2004/2005. Today’s operations face increasing complexity in data management, requiring digital solutions that go beyond traditional approaches to meet modern governance standards.
For mining and resources operations to maintain operational excellence and meet corporate governance standards, they need solutions that can manage the complexity of metal accounting across thousands of measure points. This requires automated data capture, dynamic simulation and sophisticated data validation capabilities that exceed the original scope of AMIRA P754.
Drawing on over 15 years of experience developing metallurgical intelligence software for mining and minerals operations globally, this guide explains the AMIRA P754 Code of Practice in detail. It also explores how purpose-built digital solutions enable mining and minerals organisations to achieve and exceed compliance through advanced metallurgical accounting.
Contents
- What is AMIRA P754?
- Why was AMIRA P754 created?
- The evolution of AMIRA P754 and current relevance
- What is the history of the AMIRA P754?
- Which organisations collaborated in the creation of AMIRA P754?
- What happened to AMIRA P754 after its third release in 2007?
- Which organisations are required to adhere to the P754 standards?
- How has the response been to AMIRA P754?
- What are the benefits of compliance with AMIRA P754?
- What is the structure of the AMIRA P754 Code?
- What are the consequences of non-compliance?
- How does an organisation become AMIRA P754 compliant?
- Who in an organisation is involved in driving AMIRA P754 compliance?
- Why spreadsheets are not AMIRA P754 compliant
What is AMIRA P754?
The AMIRA P754 Code of Practice for Metal Accounting provides a comprehensive framework for metal accounting governance in mining and metallurgical companies. Developed by AMIRA, an independent global industry body, it establishes standardised practices to ensure accurate, auditable and transparent metallurgical accounting.
Through its 10 core principles, the Code addresses critical aspects of metal accounting, from data collection and validation through to reporting and auditing. First released in 2005 1, with the current third release from February 2007, it has become the industry’s primary and only reference for metallurgical accounting practices.
Through its 10 core principles, the draft Code addresses critical aspects of metal accounting, from data collection and validation through to reporting and auditing.
Related: Learn more about the evolution of the AMIRA P754 Code of Practice
Why was AMIRA P754 created?
The development of AMIRA P754 was driven by the mining industry’s recognition that existing metal accounting practices were inadequate for modern corporate governance requirements. Prior to the Code’s creation, there were no standardised guidelines for metallurgical accounting, leading to inconsistent practices across the industry.
The initiative gained momentum following the 2001 ‘Challenges in Metallurgical Accounting & Information Management’ symposium in Cape Town, where industry leaders identified significant gaps in existing practices. Key concerns included:
- Lack of standardised measurement and reporting methods
- Insufficient transparency in data collection and verification
- Inadequate audit trails for metal accounting processes
- Variable quality in sampling and analysis procedures
The goal was to establish a comprehensive set of standards that could be adopted industry-wide, improving both operational performance and corporate governance.
The evolution of AMIRA P754 and current relevance
While AMIRA P754’s principles were groundbreaking when established, their importance has grown with increasing focus on corporate governance, production forecasts and planning and sustainability reporting.
Today, the draft Code’s requirements align closely with modern environmental, social and governance (ESG) compliance needs, particularly in areas of operational transparency and environmental impact tracking.
The technological landscape has evolved significantly since the Code’s establishment in 2004/2005. Modern digital solutions now enable levels of accuracy, automation and insight that exceed the Code’s original requirements, while maintaining its core principles of transparency and accountability.
Beyond compliance, implementing modern metal accounting systems aligned with AMIRA P754 principles delivers substantial operational and financial benefits through:
- Enhanced process optimisation
- Improved operational efficiency
- Better resource management
- More accurate sustainability reporting
What is the history of the AMIRA P754?
The development of AMIRA P754 spanned several years, involving collaboration between major mining companies, academic institutions and industry experts. The project produced multiple releases, with Release 3 (2007) being the current version in use today.
Key milestones in the development of AMIRA P754 1:
2001 | The ‘Challenges in Metallurgical Accounting & Information Management’ symposium in Cape Town identifies the need for standardised practices. This leads to the AMIRA P754 project, sponsored by Anglo American, Anglo Platinum, BHP Billiton, Kumba Resources and Rio Tinto. |
2004 August | Professor Peter Gaylard of UCT leads a team commissioned to develop the Code, beginning a five-year collaborative project. |
2005 October | First version of AMIRA P754 released, establishing the foundational principles for metal accounting governance. |
2006 | Second version released following comprehensive professional editing and industry feedback. Serves as a ‘beta’ version for industry testing. |
2007 February | Release of third version, incorporating 10 core principles along with detailed metallurgical and statistical methodologies across nearly 200 pages. This version remains the current draft standard. In the letter to sponsors accompanying this release, it was stated that while the Code would be a “living document”, it had reached a stage where it could be endorsed for industry use. The intention was that the Code of Practice and Guidelines would become accepted as the basis for metal accounting in the global minerals industry. |
2009 | While Release 4 was planned for distribution in 2009, extending the Code’s reach to North American mining companies, this version was never publicly released. While widely referenced, the Code has not been formally adopted by any sponsors or industry associations as binding requirements. Today, Release 3 continues to serve as the primary reference and only reference for metal accounting practices globally. |
Which organisations collaborated in the creation of AMIRA P754?
Commissioned by AMIRA, AMIRA P754 represented a collaborative effort between industry and academia. Key contributors included:
- Project leadership: Professor Peter Gaylard’s team at UCT
- Industry sponsors: Anglo American, Anglo Platinum, BHP Billiton, Kumba Resources and Rio Tinto
- Academic partners: Research teams from the Universities of Cape Town, Queensland and Stellenbosch
- Industry experts: Representatives from the South African Accounting Profession and specialists in sampling and statistics
What happened to AMIRA P754 after its third release in 2007?
While the third release indicated plans for a Release 4 in 2008, targeting wider distribution including North American mining companies, this version was not released. The project’s formal development phase concluded around 2009, though the draft Code continues to be referenced (but not enforced) as an industry standard.
Which organisations are required to adhere to the P754 standards?
AMIRA P754 establishes governance standards but does not enforce them. As a nonprofit organisation, AMIRA has no regulatory authority over industry practices. Hence no-one is “required to comply” unless driven by their own internal governance processes or external bodies.
For publicly listed mining companies, particularly those on exchanges like the Australian Stock Exchange (ASX), accurate metal accounting is crucial for production reporting and market disclosures. The ASX Corporate Governance Principles now require companies to ‘safeguard integrity in corporate reporting’ – expanding beyond financial reporting to include accurate reporting of key assets and production data.
The Code’s relevance continues to grow. AMIRA recognised early the connection between metal accounting, environmental reporting and financial reporting, stating that the Code should “facilitate full disclosure of operational performance, including losses in emissions, in line with requirements for triple bottom line reporting in financial statements.”
This alignment with corporate reporting requirements is particularly significant for ASX-listed companies, where production and metal accounting reports must undergo annual external audits by qualified metallurgists or engineers acting as ‘competent persons’. Traditional tools like spreadsheets are inadequate for meeting these governance standards.
This foresight has become increasingly significant as governments intensify their focus on ESG reporting governance. Today, metal accounting calculations form a crucial part of:
- Production reporting and market disclosures
- Financial compliance and auditing
- Scope 1, 2 and 3 emissions calculations
- Sustainability disclosures and transition planning
- ESG reporting requirements
While there may be no direct legislation enforcing metallurgical accounting governance, organisations increasingly need robust metal accounting practices to comply with sustainability and climate disclosure requirements from frameworks such as:
- Stock exchange requirements (including ASX Principle 4)
- ISSB (International Sustainability Standards Board)
- ASRS (Australian Sustainability Reporting Standards)
- CSRD (Corporate Sustainability Reporting Directive)
- SEC (Securities and Exchange Commission) climate disclosure requirements
- Internal governance requirements
- Stakeholder expectations
- ESG reporting frameworks
- Industry best practice standards
How has the response been to AMIRA P754?
Today, AMIRA P754 has gained widespread acceptance as a global standard for metal accounting in mineral processing facilities. It typically forms the basis for:
- Defined business requirements in metal accounting solutions
- Industry audit frameworks
- Process improvement initiatives
- Corporate governance procedures
- Modern ESG compliance requires adherence to AMIRA P745’s 10 governance requirements
What are the benefits of compliance with AMIRA P754?
AMIRA P754 outlines rigorous methods to understand and model plant performance and reconcile mass/energy balances. If these are successfully implemented, this results in a more detailed and accurate understanding of plant performance.
The implications and benefits of comprehensive and accurate modelling of plant performance include:
- Improved operational performance
- Better decision-making
- Enhanced financial transparency
- Increased market credibility
- Reduced risk of ESG and other non-compliance
For publicly listed companies, accurate metal accounting is particularly crucial as this data informs market disclosures, financial reporting and production forecasts.
As the Code states: “Any production operation is exposed to financial risk associated with its metal accounting process, to the extent that there is uncertainty in the evaluation of the quantities of metal delivered to that operation and produced by it. In addition, there is the risk to the reputation of a company and of negative market perceptions resulting from major metal accounting discrepancies. One of the prime objectives in the design of a metal accounting system is to enable an operation to quantify, manage and minimise the level of risk to which it could become exposed through failures or shortcomings in its metal accounting system. Each operation must conduct an initial risk assessment of its entire metal accounting system to establish and quantify the risks. The design of a metal accounting system must take these risks into consideration and set down procedures to be followed when accounting discrepancies are identified.”
What is the structure of the AMIRA P754 Code?
Release 3 February 2007 of the proposed standard comprises three broad sections:
- 10 principles (within the Code document)
- AMIRA P754 Code of Practice, Release 3 (Code document)
- Guidelines for Metal Balancing and Reconciliation, Release 3 (Guidelines document)
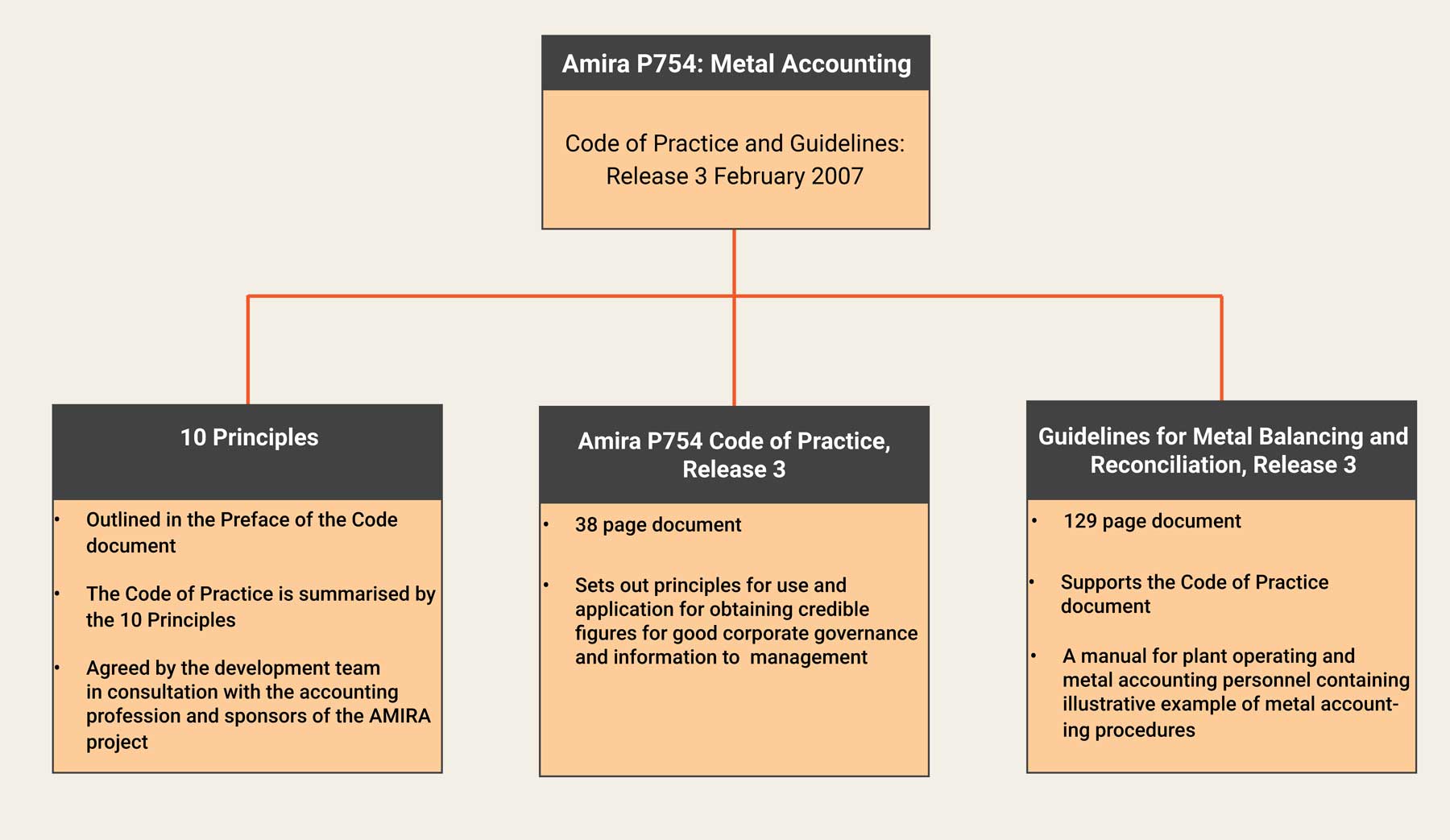
1. 10 Principles of the AMIRA P754 Code
The 10 principles form the foundation of AMIRA P754, establishing the requirements for an effective metal accounting system. Summarised below, these principles typically form the basis of defined business requirements for any metal accounting solution:
Principle 1: Measurement Systems and Data Collection
The metal accounting system must be based on accurate measurements of mass and metal content. It must be based on a full check-in/check-out system using the Best Practices as defined in this Code, to produce an on-going metal/commodity balance for the operation. The system must be integrated with management information systems, providing a one-way transfer of information to these systems as required.
Principle 2: Data Inputs and Risk Assessment
The system must be consistent and transparent and the source of all input data must be clear and understood by all users of the system. The design and specification of the system must incorporate the outcomes of a risk assessment of all aspects of the metal accounting process.
Principle 3: Documentation and Audibility
The accounting procedures must be well documented and user friendly for easy application by plant personnel, to avoid the system becoming dependent on one person, and must incorporate clear controls and audit trails. Calculation procedures must be in line with the requirements set out in the Code and must always be consistent with clear rules for handling the data.
Principle 4: Regular Auditing and Compliance
The system must be subject to regular internal and external audits and reviews as specified in the relevant sections of the Code to ensure compliance with all aspects of the defined procedures. These reviews must include assessments of the associated risks and recommendations for their mitigation, when the agreed risk is exceeded.
Principle 5: Timely Reporting and Incident Management
Accounting results must be made available timeously to meet operational reporting needs, including the provision of information for other management information systems and to facilitate corrective action or investigation. A detailed report must be issued on each investigation, together with management’s response to rectify the problem. When completed, the plan and resulting action must be signed off by the Competent Person.
Principle 6: The Use of Provisional Data
Where provisional data has to be used to meet reporting deadlines, such as at month ends when analytical turn-around times could prevent the prompt issuing of the monthly report, clear procedures and levels of authorisation for the subsequent replacement of the provisional data with actual data must be defined. Where rogue data is detected, such as incorrect data transfer or identified malfunction of equipment, the procedures to be followed together with the levels of authorisation must be in place.
Principle 7: Data Verification and Error Detection
The system must generate sufficient data to allow for data verification, the handling of metal/commodity transfers, the reconciliation of metal/commodity balances, and the measurement of accuracies and error detection, which should not show any consistent bias. Measurement and computational procedures must be free of a defined critical level of bias.
Principle 8: The Handling of Inaccuracies
Target accuracies for the mass measurements and the sampling and analyses must be identified for each input and output stream used for accounting purposes. The actual accuracies for metal recoveries, based on the actual accuracies, as determined by statistical analysis of the raw data, achieved over a company’s reporting period must be stated in the report to the company’s Audit Committee. Should these show a bias that the company considers material to its results, the fact must be reported to shareholders.
Principle 9: Inventory Verification
In-process inventory figures must be verified by physical stocktakes at prescribed intervals, at least annually, and procedures and authority levels for stock adjustments and the treatment of unaccounted losses or gains must be clearly defined.
Principle 10: The Handling of Bias
The metal accounting system must ensure that every effort is made to identify any bias that may occur as rapidly as possible and eliminate, or reduce to an acceptable level, the source of bias from all measurement, sampling and analytical procedures when the source is identified.
Note regarding exception reporting:
The Code makes provision for exceptions, stating that “It is possible that, in older metallurgical operations, it may be physically impossible or very expensive to implement all of the above principles, in which case the Code stipulates that an Exception Report must be submitted for approval by a Competent Person as well as by management.”
2. AMIRA P754 Code of Practice, Release 3, 2007
Beyond the core principles, the Code of Practice provides comprehensive guidance for implementation. This 38-page document was developed as a key deliverable of the AMIRA P754 Project, intended to serve as a global standard for best practice metal accounting.
The Code outlines methods for obtaining credible figures, including their bias and precision, and facilitates full disclosure of operational performance. This includes losses in emissions, aligning with requirements for triple bottom line reporting in financial statements.
Notably, this Code demonstrated significant foresight by linking accurate and credible metal accounting with sustainability reporting – a connection that has become increasingly relevant with modern requirements such as the Australian Sustainability Reporting Standards (ASRS S1 and S2) created by the Australian Accounting Standards Board and enforced by ASIC.
While the Code focuses on metallurgical plant feed as its starting point, rather than mining operations, it provides detailed requirements across key areas summarised in the table below.
The principles of the metal accounting system discussed in the Code document are summarised in the table below.
Table: Summary of the principles of the metal accounting system outlined in the AMIRA P754 Code document | |
Data Management Data Acquisition/ Entry Data Documentation |
|
Mass Measurement Accuracy and Precision of Mass Measurement (Scales/Weighing Equipment, Flow Meters) Methods of Measuring Mass |
|
Sampling Accuracy and Precision of the Sampling System Multi-Stage Sampling Systems Sample Storage Sample Labelling |
|
Sample Preparation and Analysis Sample preparation includes moisture determination, sample reduction, sample mixing, sample division, sample storage after sample reparation Analysis |
|
Stocktakes |
|
Metal Balancing The Metal Accounting Process Metal Balancing Applications Mass Balancing for Environment and Health Monitoring Mine to Product Balancing and Reconciliation |
|
Reporting |
|
Selection and Use of a Competent Person | For the purposes of the Code, a Competent Person must be a member of the professional registration authority recognised by the Code administrators and have a minimum of 5 years’ experience relevant to the metal or mineral under consideration of the type of operation involved. The Competent Person must (page 25 AMIRA P754 Code 2007):
|
Design of Metal Accounting Systems |
Page 26 of the AMIRA P754 Code states the metal accounting system must include the following:
New plants must include in their scope the design of the accounting system, with identification of mass measurement and sampling points required to determine a reliable metal balance. Detail to installation, calibration, maintenance and routine operation must be considered. If these requirements cannot be met and steps can’t be taken to comply, an approved Exception Report is required. |
Metal Accounting Auditing Rules Audit Team and its Responsibility Metal Accounting Review Physical Audits |
|
Source: AMIRA P754 Code of Practice, Release 3, 2007
3. Guidelines for Metal Balancing and Reconciliation, Release 3, 2007
The Guidelines document expands on the Code of Practice, providing detailed instructions on implementation. This comprehensive 192-page manual is designed for plant operating and metal accounting personnel, offering practical guidance on applying the Code’s principles. The document includes:
- Detailed technical procedures
- Practical implementation examples
- Glossary of technical terms
- Reference materials
- Illustrative metal accounting procedures
What are the consequences of non-compliance?
As stated above, unless an organisation is bound by legislation or standards from a governing body, there are no legal or direct consequences of non-compliance with AMIRA P754.
However, the standards exist for a reason, with non-compliance potentially resulting in:
- Lack of operational transparency
- Reduced ability to verify data accuracy
- Limited process optimisation capabilities
- Poor financial performance due to inefficient operations
- Increased risk in financial reporting
- Challenges meeting modern ESG requirements
How does an organisation become AMIRA P754 compliant?
The journey to becoming AMIRA P754 compliant begins with having sufficient buy-in at multiple levels of an organisation. A critical mass of stakeholders needs to become sufficiently aware of the benefits of P754 compliance and driven to make the required investment into the systems, processes, technology, and personnel training involved in becoming compliant.
The recommended pathway includes four key steps:
- Feasibility Study
Understanding current processes and requirements, reviewing existing instrumentation and workflows and creating an implementation plan. - Implementation
Deploying automated data capture, quality analysis and dynamic simulation configured to site-specific requirements. - Training, Support and Maintenance
Providing comprehensive training, expert support and ongoing system maintenance to ensure sustained compliance. - Extension Modules
Enhancing functionality with additional capabilities for process optimisation and reporting.
For detailed implementation guidance, digital solutions and a complete roadmap, refer to Metallurgical System’s solutions page for AMIRA P754 compliance.
Who in an organisation is involved in driving AMIRA P754 compliance?
Becoming compliant with the AMIRA P754 Code of Practice requires engagement across multiple organisational levels. Key stakeholders mentioned in the Code include:
- A “Competent Person” – A person with suitable qualifications and experience to undertake a review of the design and the performance of the metal accounting system and balance
- Senior corporate and operational management
- Independent Directors
- Members of the Risk/Audit Committee
- Project design staff (including outside contractors)
- Plant operation staff
- Laboratory staff
Why spreadsheets are not AMIRA P754 compliant
When AMIRA first released P754 in the early 2000s, the primary option for data collation and reporting was spreadsheet tools like Microsoft® Excel. As a result, organisations attempting to become P754 compliant would use manual spreadsheets to analyse and reconcile their data.
However, spreadsheets present several critical issues when used to meet P754 standards:
1. Lack of consistency and transparency to source data
One of the biggest risks in any organisation is that compliance reporting or data will be manually manipulated, either intentionally or in error. It’s why AMIRA P754 principle #2 stipulates that a compliant metal accounting system “must be consistent and transparent, and the source of all input data to the system must be clear and understood by all users of the system.”1
The metal accounting data within spreadsheets can rarely be automatically and accurately traced back to its source, such as lab assays or a plant historian. It is also unprecedented that this has been achieved over any time period as personnel changes. Simply labelling a column, running a macro and assuming the data has been transferred accurately does not make for a transparent system. Even spot checks cannot be considered a reasonable check due to the volume of data which plants hold, and the ability to manually omit or overwrite values.
Typically, in this environment, the metal accounting numbers are generated and then checked by various people, each of whom may make changes to different versions of the spreadsheet based on requirements of the day, with the declared result bearing little resemblance to the source data.
In a typical mineral processing plant that uses spreadsheets for metal accounting, there is simply no way of knowing that the data you are submitting as compliant to governance standards reflects plant source data with any degree of accuracy. In fact, when using spreadsheets, data and formulas can be modified anonymously at any time, and without a trace. While integration with source data to spreadsheets is possible, information can still be very easily altered without a record. This can have significant consequences, as was illustrated when Katanga Mining was investigated by the Ontario Securities Commission in 2018. 2
Being able to trace the source of every identified issue is vitally important. Even a small amount of product being lost to tailings, or unnecessary overdosing of reagent on an ongoing basis can, for instance, become very costly very quickly. Equally, being able to use actual plant data to identify when a piece of plant equipment needs maintenance, rather than simply relying on scheduled maintenance, can also translate into huge cost savings.
As a result, it’s important that any metal accounting system is fully traceable and enables plant management to very quickly isolate the source of a problem, or potentially the point at which an error in a formula has been made. Spreadhseets unfortunately do not offer this capability.
2. Limited analytical scope
The volume of data within a typical minerals processing plant is enormous, complex, multi-faceted and ever-growing. Emerging requirements to analyse, often, billions of rows of production data from increasingly complex plant instrumentation extends well beyond the scope of a spreadsheet.
AMIRA P754 principle #7 stipulates that a compliant Metal Accounting system “must generate sufficient data to allow for data verification, the handling of metal/commodity transfers, the reconciliation of metal/commodity balances, the measurement of accuracies and error detection, which should not show any consistent bias.” 1
Although spreadsheets can certainly be configured to include calculations, they are not capable of storing enough source data to complete detailed verification. They are also incapable of generating sufficient cross-check data without any user intervention and, in fact, rely on user discretion, which is a more significant issue.
3. Inaccuracy and lack of error control
Another major problem with spreadsheets as a metal accounting platform is that they lack in-built error control. There is no debugging capability, and no way of instantly knowing if and where an error has occurred. This is non-compliant with AMIRA P754 principle 1, requiring accuracy 1.
One study suggests that 88% of spreadsheets include errors 3. Another well-documented spreadsheets failure case in financial services, known as the ‘London Whale’, directly resulted in losses of several billion dollars by JP Morgan, leading to suggestions of spreadsheets being the “most dangerous software on the planet”4.
The Forbes article on this subject says: “Both the Switzerland-based Basel Committee on Banking Supervision1 (BCBS) and the Financial Services Authority2 (FSA) in the UK have recently made it clear that when relying on manual processes, desktop applications or key internal data flow systems such as spreadsheets, banks and insurers should have effective controls in place that are consistently applied to manage risks around incorrect, false or even fraudulent data.“ 4
Similarly, in mineral processing, if the wrong figure is accidentally entered into a particular cell, or there is an unknown issue with a formula calculation, it can render the analysis or reporting completely incorrect, which can have very far-reaching consequences for the operation.
Metallurgical Systems’ Managing Director, John Vagenas, having regularly seen similar disasters in plant spreadsheet use, has often spoken publicly about the issues associated with over-reliance on spreadsheets in the minerals processing sector:
“When it comes to reporting a plant’s performance, one of the biggest problems with spreadsheets is that there is absolutely no way of knowing at-a-glance whether the data you are seeing is accurate. This poses a major problem for AMIRA P754 compliance. Using spreadsheets is suitable when your data is simple and easily cross-referenced. This is no longer the case in a modern mineral processing facility where data is extremely complex and ever-changing… Only after the extent of flawed investment decisions, inaccurate compliance reporting and drastically more expensive processing costs are revealed to a plant management team, stemming from the use of spreadsheets, does the real cost of using spreadsheets for plant decisions and reporting become apparent.”
4. Limited re-use and scalability
In metallurgical facilities, reporting is ongoing and frequent. Regular and ad-hoc reports need to be quickly and constantly provided on all aspects of a plant’s operations. However, when using spreadsheets, there’s very limited re-use of data, or ability to scale the spreadsheets based on growth or changes in the plant’s facilities. Spreadsheet do not store formulas in a central location, which limits its scalability.
Compiling a new report will often involve the author cutting and pasting data from one tab on a spreadsheet to another. If formulas are accidentally altered during this exercise, it can be hard to tell, and there is enormous precedent for data to be incorrectly reported. Similarly, continuous new report creation in spreadsheets is time consuming and laborious, distracting skilled metallurgists from the main focus of their job.
In an article on LinkedIn, mining consultant Xavier Hill suggests that, because of this inaccuracy, it’s “time to ban” Excel spreadsheets for mining studies. “Excel is great because it is easy to use, you do not need to code (apart from maybe some Visual Basic) and is fantastic for simple assignments. The problem is when we use it beyond what it is really intended for. Enormous spreadsheets with complex formulas spreading over a range of tabs become next to impossible to audit and it only takes one mistake for the rest of the data and the conclusions drawn from it to be wrong,” 5 he says.
5. Lack of automation
When a plant is using spreadsheets for its metal accounting platform, it is typically reliant upon a small group of people – or even one operator – who understands the formulas within the spreadsheets and how they can be used and interpreted. The more complex the spreadsheets, the greater likelihood that they will be maintained by a single, dedicated specialist. If this particular person is away, or leaves the business, the overall metal accounting function can be seriously impacted. This directly contravenes AMIRA P754 principle #3 1.
In addition, the mundane and manual spreadsheets daily operational reporting tasks often assigned to skilled plant metallurgists are typically time intensive, and prevent more value-added tasks from being performed, which are more conducive to their skillset.
6. No machine learning or artificial intelligence generated insight
A major disadvantage of relying on spreadsheets for metal accounting is that, unlike advanced digital twin solutions which utilise machine learning and artificial intelligence, they cannot provide a plant’s management team with any automated insights. Nor can they drive automated improvements. The level of insight that a spreadsheet can offer is very one-dimensional and relies upon the interpretive power of those managing the spreadsheets or reviewing reports.
While a spreadsheet may be a sufficient way of managing and interpreting a small pool of data, its capacity to analyse and provide insights for large datasets, and ongoing analysis, is very limited.
“As margins within our industry continue to decline, the accurate accounting of costs, revenues, resources, reserves, and capital becomes even more critical… the time has come to ban spreadsheets for large datasets…,” says Hill 5.
7. Auditability
AMIRA P754 principles #3 and #4 1 both require a clear audit trail to be available. They also require that the metal accounting system must actually be subject to internal and external audits.
We have demonstrated the inability of spreadsheets to produce data traceable to source systems. This has the associated effect of being equally unavailable to be easily audited, resulting in non-compliance to these AMIRA P754 principles.
8. Lack of ‘what if’ planning
The AMIRA P754 principles exist to drive continual improvement in the metal accounting discipline. For individual plants, this can translate to being able to predict future processing scenarios and place the plant’s management in a position to make the necessary adjustments to improve processing performance over time.
While spreadsheets do support this ‘what if’ planning to an extent, it doesn’t allow the operator to compare multiple scenarios at the one time. Each individual scenario will often require its own spreadsheet. This limits the extent to which plants can use data to achieve continual just and ongoing improvement.
9. Spreadsheets as a relational database
To obtain a robust and detailed understanding of a mineral processing plant, and comply with AMIRA P754 principle #2 1, plant analysts need to collect and analyse data from right across the plant, from a number of data sources, and of several data types and formats.
Bringing all of this information together, and consolidating it, is what provides plant management with true plant operational performance visibility. While spreadsheets can integrate with some external databases and tools, its ability to capture, merge and relate huge amounts of data from various unrelated sources is very limited.
The formulas within spreadsheets are also very non-portable and proprietary, which means it is very difficult, if not impossible, to use spreadsheets as a data source in itself. However, many try to use spreadsheets as a database in this manner, continuing to stretch it to lengths with which it has been shown to struggle.
Related article: Why Excel is not AMIRA P754 compliant
What are the common challenges in implementing AMIRA P754?
Technical challenges when implementing AMIRA P754 span from the initial stages (when current processes are reviewed/audited) through to implementation and ongoing maintenance.
From reporting and compliance to maximising efficiency, everything is underpinned by having access to accurate and up-to-date data. The complexity of these challenges requires a shift in organisational culture across people, process, technology and data.
Data management presents particular challenges that cut across process and technology areas. The ability to collect, validate and analyse data effectively is fundamental to successful AMIRA P754 implementation.
People
Metal accounting is often viewed as ancillary to plant operation and handled by junior inexperienced staff. However, qualified technical staff are required as metal accounting feeds directly into financial accounts and corporate governance.
The Code relies on a Competent Person to ensure data is correctly measured, handled and utilised. If requirements cannot be met, an Exception Report must be signed off by the Competent Person and submitted to the Audit Committee or Board, detailing deviations and associated risks.
Finding suitable Competent Persons presents significant challenges as they must:
- Be independent from operations
- Have suitable qualifications and experience in metal accounting
- Make recommendations for system design
- Take responsibility for final approval
- Conduct periodic reviews and audits
- Monitor action plans to remedy faults
- Submit compliance reports to management
The organisation requires engaged management, a curious, experienced and technical Board of Directors and Audit Committee to fully understand their duties and responsibilities of AMIRA compliant processes and the risks and financial loss from non-compliance.
Process
It is important to understand the components of the metal accounting system. The AMIRA P754 Code outlines best practice processes for all components such as mass measurement, sampling and sample management, analysis, data management, metal balancing and reconciliation methods, reporting and auditing.
Diagram: Metal accounting system structure
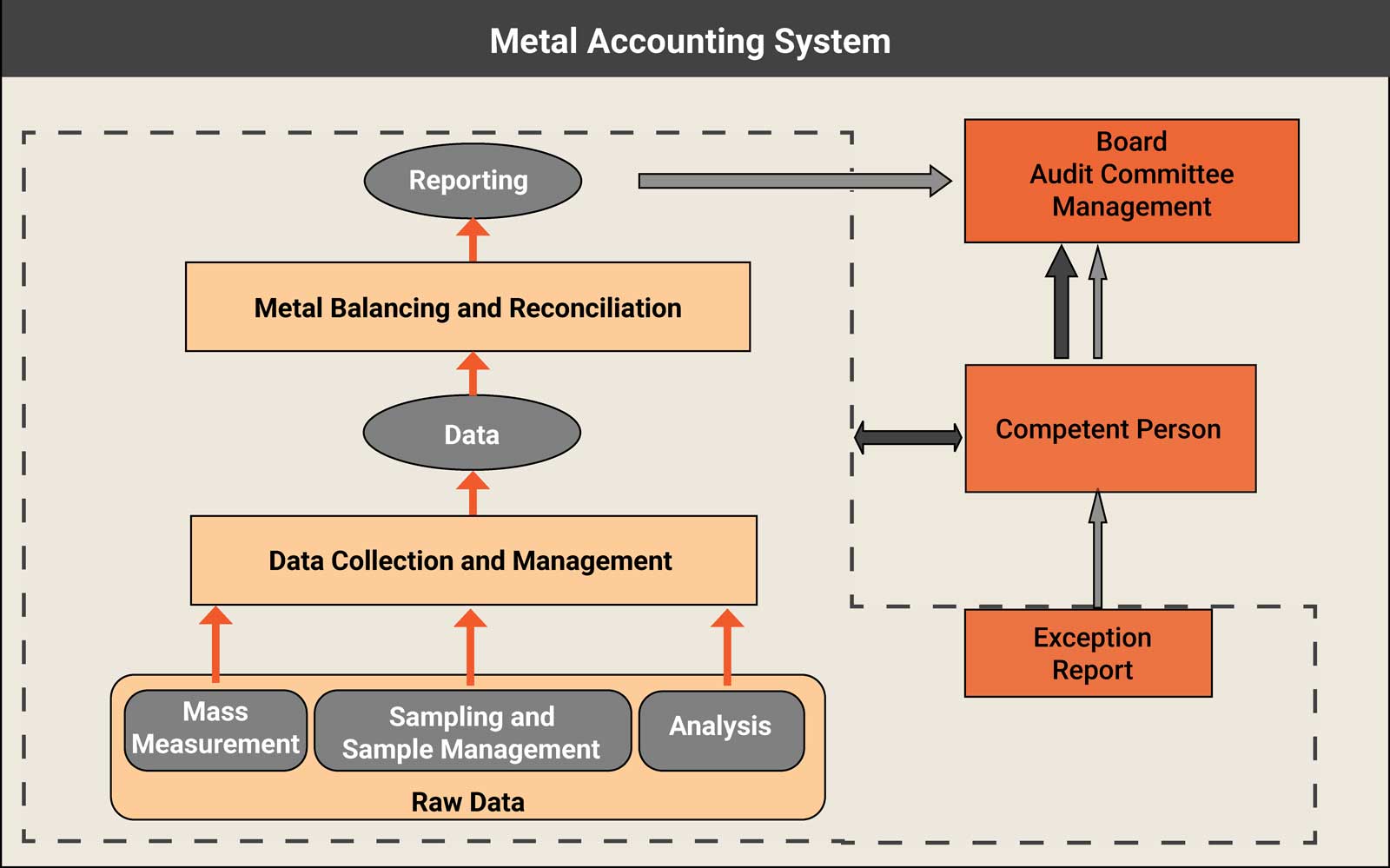
Technical challenges with process include:
- Lack of standard metal accounting procedures, as each process is different with varying levels of complexity
- Lack of awareness about required precision in mass measurement, sampling and analysis
- Inadequate mass measurement and sampling from poor equipment specification, installation, and maintenance
- Data management issues where data manipulation can occur without proper approvals
- Using inconsistent methods for metal recovery calculations
- Reliance on traditional statistical data reconciliation that spreads errors across streams rather than using digital tools to identify error sources
Technology
AMIRA P754 was published in 2007, and while its principles remain foundational, the technological landscape has transformed dramatically since 2004/2005. Modern solutions now enable capabilities that far exceed what was possible when the Code was written.
Traditional approaches typically use:
- Periodic sampling to estimate metal content
- Bulk measurement of inputs/outputs
- Manual data collection and record keeping using spreadsheets
- Basic software tools with low data resolution
- Statistical Data Reconciliation (SDR methods) with errors not properly accounted for
- Limited reporting frequency and minimal automation
Modern technology, particularly digital simulation, can address these limitations by:
- Contextualising data and filling gaps
- Measuring all process streams using time as a dimension
- Comparing calculated vs measured data to flag alignment issues
- Enabling secondary metallurgical accounting for sites with limited instrumentation
- Supporting complex process chemistry calculations
Diagram: Components of metal accounting controlled by digital software and site personnel
This Venn diagram illustrates which aspects of modern metal accounting can be managed by digital software, which require site control and which require an integration of both.
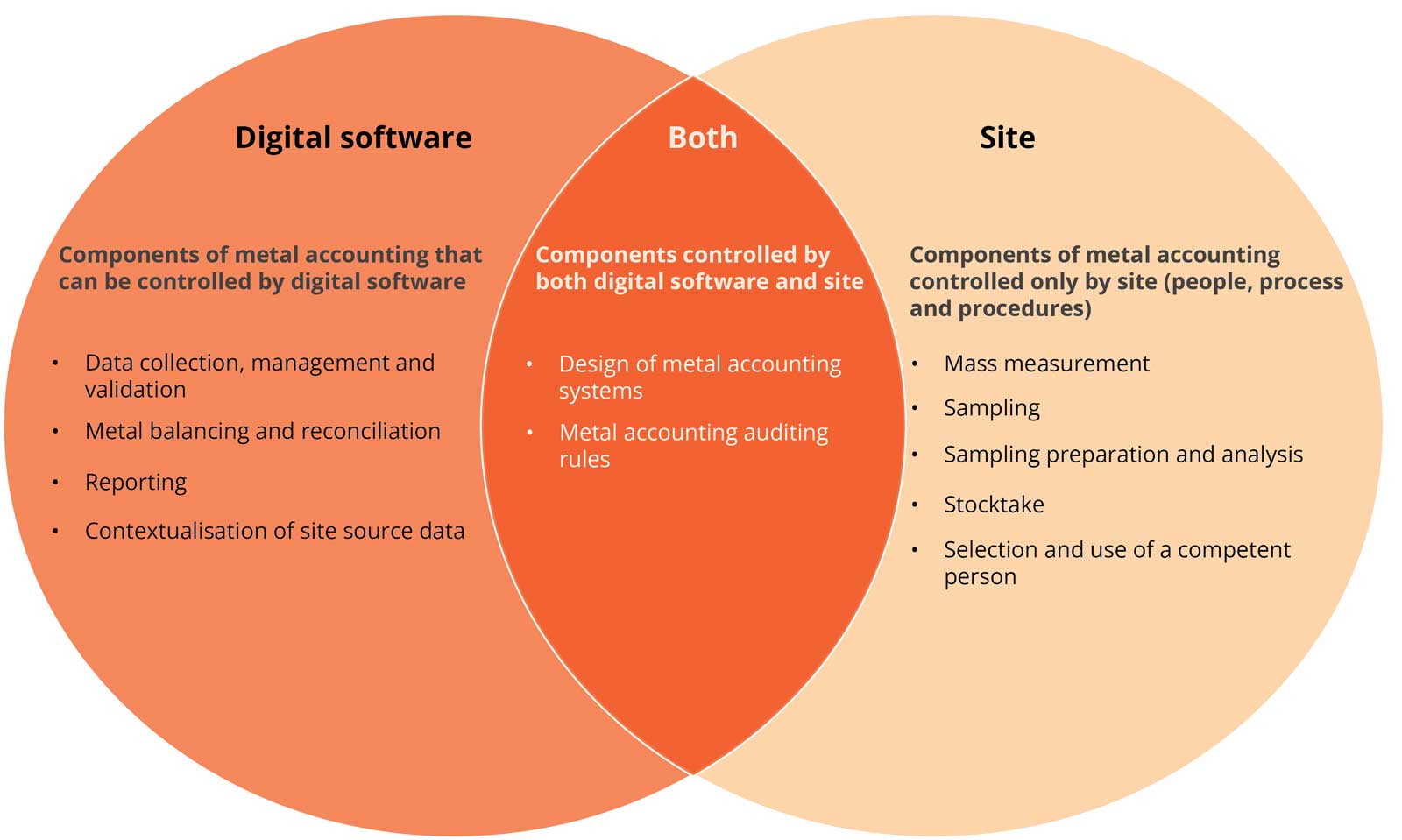
Mass measurement, sampling, sampling preparation and analysis, stocktake procedures, selection of competent persons, calibration of instruments and general site housekeeping all fall within the control of the process and procedures of the site. However, digital software can automate data collection and validation, run multiple iterations of metal balancing and reconciliations, produce automated configurable reports and contextualise source data. The design of the software contributes to the requirements of the entire metal accounting system, auditing rules and procedures can be configured and built into structured workflows and approval processes.
Overcoming data challenges
Modern digital solutions automate the data collection process completely, ensuring data is collected consistently from the same sources at the same times, without manual intervention or interruption.Quality Control
Data evaluation incorporates automated quality control and assurance (QAQC) steps that:- Evaluate all incoming data against consistent rules for each phenomenon (mass flow, volumetric flow, density, metal grade, concentration)
- Flag and record data outside acceptable ranges for quality analysis
- Enable identification of measure points with consistent outlying values
- Allow customised quality limits for individual data points
- Maintain data integrity while avoiding unnecessary elimination
Dynamic Mass and Energy Balance
This powerful approach to metallurgical accounting:- Takes diverse plant information as inputs for full process simulation
- Includes all flows, chemical reactions and inventory changes
- Generates significantly more data than what is fed into it
- Calculates previously unmeasurable elements like mass transfers and inventory changes
- Reports at an hourly level for improved statistical significance
- Enables analysis of thousands of data points over time
- Element-by-element flow analysis
- Performance metrics calculation
- Real-time efficiency monitoring
- Comprehensive inventory tracking
- Statistical analysis of thousands of data points
Data Validation
The system provides robust validation through:- Comparison of calculated data against original plant data
- Large-scale quality control analysis across multiple inputs
- Clear identification of objectively inaccurate data
- Root cause analysis capabilities
- Validation of data representativeness in context
- Identifying unmetered dilution effects on concentration assays
- Detecting undocumented process changes
- Confirming data representativeness in context
Data Security and Access Control
To ensure data integrity and confidentiality, the system implements:- User authentication with role-based access permissions
- Secure data encryption
- Regular software updates and patches
- Robust network security configurations
- Automated data backup procedures
The future beyond compliance: The business case for modern metal accounting
The business case for implementing modern metal accounting technology extends far beyond compliance. As demonstrated in numerous case studies, MI Core® implementations have helped mining and minerals operations recover millions in lost production through improved process efficiency and prevention of product losses.
As organisations face increasing pressure around sustainability reporting, MI Core®’s validated, traceable activity data also enables both ESG framework compliance and informed climate transition planning. With new global sustainability legislation requiring detailed environmental impact reporting, having a single source of truth for operational data ensures accuracy in climate disclosures while streamlining reporting processes.
By implementing modern metal accounting technology like MI Core®, organisations not only exceed AMIRA P754 requirements but also position themselves to meet future challenges around financial optimisation and sustainability reporting.
MI Core®’s digital twin technology is designed to exceed all AMIRA P754 principles through advanced data validation and dynamic simulation capabilities.
Going beyond traditional approaches, it delivers unprecedented levels of transparency and accuracy in metallurgical accounting. From automated data capture and mass measurement to inventory tracking and bias detection, MI Core® enables both comprehensive compliance and operational optimisation.
Learn more: Explore how MI Core exceeds each AMIRA P754 principle
Frequently Asked Questions about AMIRA P754
What is a Competent Person under AMIRA P754?
According to the AMIRA P754 Code of Practice (Release 3), a Competent Person must be:
- A member of the relevant local professional registration authority, or other recognised statutory body
- Independent from the operation concerned
- Have minimum five years’ experience relevant to the metal/mineral and operation type
Key responsibilities include:
- Formal appointment by management to recommend and audit metal accounting reporting systems
- Final approval of metal accounting system design
- System auditing after installation
- Conducting periodic compliance reviews
- Problem investigation and monitoring
- Reporting to management on compliance and remedial actions
Source: AMIRA P754 Code of Guideline Release 3, page 25
Is AMIRA P754 compliance mandatory?
AMIRA P754 establishes governance standards but does not enforce them. While compliance isn’t legally required, some organisations choose to follow these standards to improve operational performance, enhance financial transparency and meet modern ESG reporting requirements.
Why was AMIRA P754 created?
AMIRA P754 was developed in response to the mining industry’s need for standardised metal accounting practices. Before its creation in 2005, there were no official guidelines for metallurgical accounting, leading to inconsistent practices across the industry.
How has AMIRA P754 evolved since its creation?
While the principles established in 2004/2005 remain foundational, technological capabilities have advanced significantly. Modern digital solutions now enable levels of accuracy, automation and insight that exceed the Code’s original requirements while maintaining its core principles of transparency and accountability.
What are the main benefits of AMIRA P754 compliance?
Key benefits include:
- Improved operational performance
- Better decision-making capabilities
- Enhanced financial transparency
- Increased market credibility
- Stronger compliance with ESG requirements
Take control of your AMIRA P754 Metal Accounting
To learn how MI Core® can help you achieve AMIRA P754 compliance while optimising your metallurgical accounting processes, contact our expert team on +61 2 7229 5646 or info@metallurgicalsystems.com
About the authors
This article has been collaboratively authored by the team at Metallurgical Systems, and fact-checked and authorised by Managing Director and industry specialist John Vagenas.
References
- AMIRA P754: Metal Accounting Code of Practice and Guidelines: Release February 2007
- Ontario Securities Commission, Press Release
- Marketwatch: 88% of spreadsheets have errors
- Forbes article Microsoft’s Excel Might Be The Most Dangerous Software On The Planet
- Xavier Hill, LinkedIn: It’s time to ban Excel for mining studies