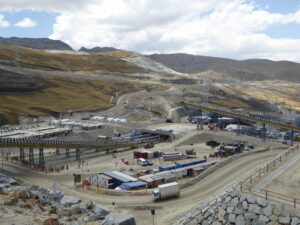
Using a steady-state plant simulation model, MI Scenario® enables you to use data from your digital twin, sourced from across your plant, in order to determine likely future processing outcomes. Thanks to powerful metallurgical processing scenario testing, you can adjust input figures to determine how specific adjustments in variables like feed grades or throughput will affect final product and plant recovery. In addition, by modifying your plant’s historical data or making changes to your plant flowsheet, you can create and compare scenarios using cutting edge reporting and data analysis tools. The results from these simulations automatically flow into MI Core® to help you manage metallurgical production budgeting and forecasting, set targets and compare theoretical results to actual plant performance.